Most livestock farmers are aware of the benefits of utilizing feed-processing equipment such as grinder mixers and TMR mixers. In fact, many are already using that equipment. But there are also pockets of opportunity to cultivate first-time buyers who, for a variety of reasons, are looking to take better control of their feeding operations.
In the case of a TMR mixer, the ability to combine high-forage content with grain and supplements allows farmers to provide the nutrition their animals need to maximize their potential.
“TMRs typically have a scale so the farmer knows just how much feed an animal is getting,” says Jay Monson, store manager at Johnson Tractor’s Baldwin, Wis., location, which carries Supreme International and Meyer TMR mixers, along with grinder mixers from H&S Mfg. and Art’s Way. “The feed is also more palatable because it’s broken down and mixed so well. The cow will actually eat almost everything instead of sorting through the ration.”
Not all TMR mixers are created equal, though. First of all, there are two general types. Mike Countryman, a product specialist with distributor Cummings & Bricker, says horizontal mixers are best suited for higher-grain rations with less forage, making them a good option for beef producers. Vertical mixers, on the other hand, are ideal for higher-forage rations, making them a good option for dairy farms and cow/calf operations.
Dealer Takeaways
- There is a well-developed market for TMR mixers and grinder mixers that is regularly looking to replace and/or upgrade existing equipment. Offering options and providing demos are key to converting sales.
- There is also an opportunity to cultivate first-time buyers by identifying how some farmers are looking to take better control of their feeding operations.
- It’s not uncommon for livestock farmers raising ruminants to invest in both a TMR mixer and preprocessing equipment like grinder mixers and forage processors.
- A consistently uniform mix is what buyers scrutinize most, followed closely by design features that make a machine more efficient and durable.
- Dealers report that their customers are almost always pleased with the ROI of investing in this type of equipment, which results from a combination of increased milk production or overall animal health, reduced cost and aggravation tied to inconvenient feed delivery times, reduced cost from processing their own grains and forages, and increased control over feed quality.
“If you feed 1-2 pounds of dry hay per animal per day, a horizontal mixer can handle that,” Countryman says. “But if you feed 10 pounds, like if you’re feeding round bales and some grain, you’re going to have issues. A horizontal mixer is not designed to handle that much long forage.” Cummings & Bricker serves dealers throughout the Northeast, Mid-Atlantic and Midwest. Product lines include Jaylor TMR mixers, Teagle bale processors and Weaverline TMR choppers.
Mix Consistency is Critical
Regardless of which type of TMR is chosen, dealers should focus on design features that speak to the delivery of a high-quality mix.
In the case of Jaylor vertical mixers, for example, a unique auger design helps deliver a final mix that’s ideal for dairy farms. It’s referred to as a square-cut auger, as opposed to the typical auger that has rounded edges. Additionally, several knives are strategically placed around the auger. “That makes the mixer very effective at processing long-stemmed forages down to a size where the cow doesn’t want to sort it out,” says Scott Brown, sales manager at Cummings & Bricker.
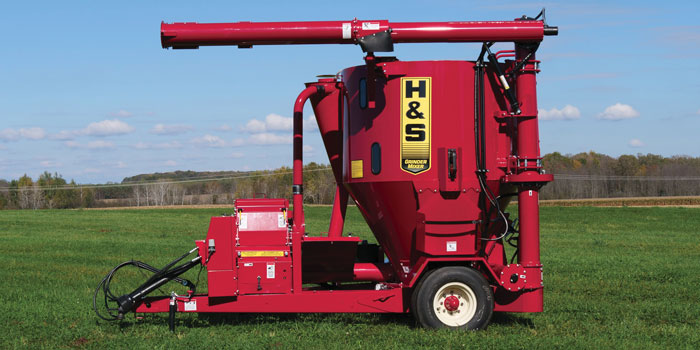
The GM9117 Grinder Mixer from H&S Mfg. has a 167-cubic-foot capacity. A 14-inch mixing auger with a 30-inch base helps ensure superior mixing uniformity. A side-mounted supplement hopper allows the addition to other ingredients to improve the quality of the final mix. H&S Mfg.
Dennis Schams also liked to spend time talking about the auger on a vertical mixer. He was a standout sales rep for St. Joseph Equipment in La Crosse, Wis., for many years before he retired in 2023. Willem van der Kooi, a territory sales manager with Supreme International, says Schams sold an average of 12 vertical mixers a year while working for St. Joseph Equipment, which has since been acquired by Johnson Tractor.
“Some mixers have an auger shaped like a Christmas tree,” Schams says. “The kicker plate sends feed toward the center of the auger. But as that feed travels up the auger, which keeps getting narrower, feed starts falling off. The bottom half of the feed ends up getting over mixed.”
In the case of the Supreme International vertical mixers, Schams says a multi-patented auger is uniquely designed with wider, uniform flighting that allows more feed to carry up through the center of the auger to the top. That enables more uniform mixing.
As Schams reminds, the whole reason for using a TMR mixer is to ensure that each animal gets precisely the right amount of nutrition. To that point, he also liked to talk about the weighing options on a mixer.
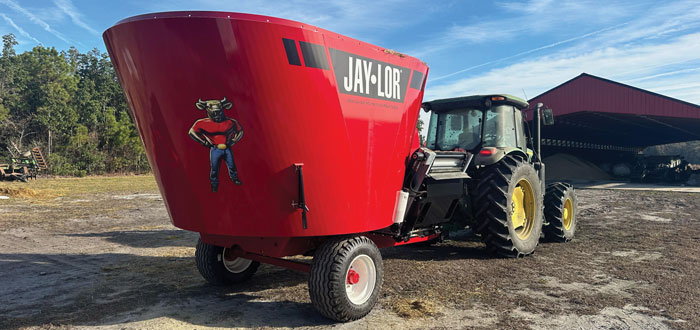
The Model 5425 single-auger TMR from Jaylor features the company’s unique square-cut auger with sloped top, along with a series of tungsten carbide-coated knives. These features help process long-stemmed forages down to a size where the cow won’t attempt to sort it out of the ration. Jaylor International
“The scale is an under appreciated feature,” Schams says. “If the recipe isn’t correct, the farmer could actually kill a cow. Some manufacturers still have their load cell on an axle or the hitch. But then every bump can affect the measurement. Supreme always has all four load cells on the frame, and then mounts the tub to that. That way, all the scale has to do is feel the weight of the mixer, so it’s more accurate. Other manufacturers have begun doing it this way, too, but not everyone. So it’s important to touch on scale accuracy with the customer.”
Because TMR mixers have been such a household machine on dairy and cattle farms for many years, Monson says most customers come into his store with a specific product in mind. They are often expanding their operation and in need of a larger unit, or simply replacing an outdated unit that isn’t mixing so well anymore. Demos are key to closing the sale.
“Then they can try the machine out, and ask their nutritionist or herd manager to take a look at how well the ration is being mixed,” Monson says. “They can do a shaker on it to check the particle size, and compare the overall mix to what their current unit is producing.”
Other Talking Points for TMR Mixers
It’s also important to discuss production needs with the customer. How many animals are they looking to feed? Do they want to feed with 1 load, or are they willing to do several loads? This information will help focus in on the appropriate size range.
Schams followed a sizing formula. For a cow to produce 100 pounds of milk per day, it has to eat at least 100 pounds of food per day. That translates to nearly 5 cubic feet of food per cow. “If the farmer has 200 cows, he’ll want a mixer with a minimum 1,000-cubic-foot capacity to feed them in 1 load,” Schams says.
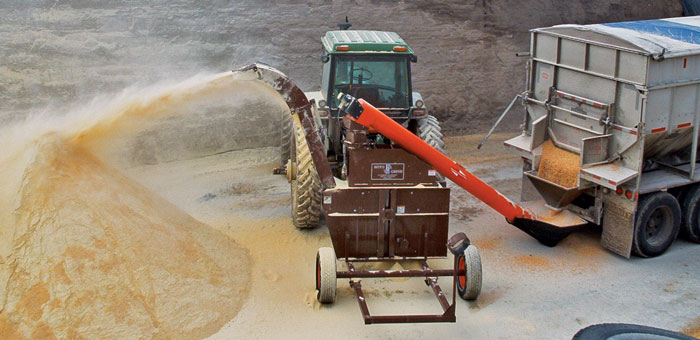
Roto Grind says its grain grinders are capable of grinding any type of small grains, either dry or high moisture, for less money than a roller mill or conventional-style hammer mill. The Model GG7 is a 7-foot machine that can produce 20-40 ton per hour. Pictured here is the Model GG10, capable of 35-60 ton per hour, if not more. Roto Grind (Burrows Enterprises)
The dealer should also ask the customer how they want to load their mixer. “Some mixers are pretty tall,” Schams points out. “If the farmer wants to load with a small skid steer, that could be a problem. But they may also have a tractor-loader or maybe even a compact wheel loader. That would open up their options.”
It’s also important to find out if the farmer will be putting the ration on the ground or into a bunk. As Schams explains, some TMR mixers have a limited discharge height.
Customers can also choose between pull-type, truck-mount and stationary units. In Schams’ experience, most farmers want a pull-type so they can use their tractor. But a truck-mount could be considered if the farmer wants more speed when traveling from feeding station to feeding station, and perhaps farm to farm. A stationary unit might make sense for a larger farm that wants to run a 2-person feeding operation with 1 person mixing the ration while the other delivers it to the animals. “The entire operation can be sped up that way because 1 person working alone will spend at least 20 minutes just loading up the mixer,” Schams says.
Efficiency is an important topic to discuss in general. Dealers should ask about the farmer’s tractor and horsepower. “Sometimes a TMR can mix in 3-5 minutes, and sometimes it will take 15-20 minutes,” Brown points out. “That all plays into horsepower requirements, fuel consumption and time spent mixing.”
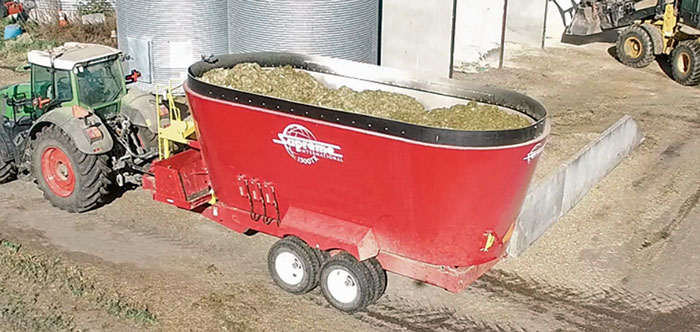
Supreme’s 1500TR Vertical Mixer features the same durable planetary drive and gearbox as other models. This model is at the larger end of Supreme’s product line. It has a maximum payload of 50,000 pounds and requires 200 hp. Supreme International
Facilities also come into play. Brown says dealers should find out if the customer has a drive-thru feed alley and, if so, which side of the tractor they need to feed to. Having the right size and configuration will help speed up feeding operations.
“If a farmer does 3 mixes a day and can save 7 minutes per mix, they’ll save 127 hours a year,” Countryman points out. “What’s that worth to their bottom line, because they’re paying somebody to mix that feed.”
Another thing that impacts the bottom line is mixer reliability. That’s why Schams always took the time to walk through features that make a machine more durable. He says most dairy farms are in replacement mode when their current TMR is 5-8 years old.
Pockets of Potential for New Feed-Processing Equipment Sales
Whether you’re talking cattle, hogs, goats or chickens, livestock farmers all have one thing in common. They have to feed their animals, and their financial success hinges on animal health and productivity as much as anything.
It’s hard to find a farmer who doesn’t understand that. It’s nearly as difficult to find one who isn’t aware of the various feed-processing equipment that’s available. In fact, it’s not always easy to find a farmer who doesn’t already own some machinery.
A big piece of the market is farmers who are looking to replace an existing piece of equipment, or perhaps upgrade to something larger as their operations grow. But that’s not to say there aren’t opportunities to cultivate first-time buyers. There may also be opportunities with farmers who are looking to add new types of feed-processing equipment to their operations.
Finding Farmers with a Need for a TMR
One equipment distributor has witnessed a market expansion for TMR mixers in particular. While the primary customer segment is dairy farmers, other segments are catching on. Dealers servicing diversified markets have ample opportunity to sell this type of equipment.
“Many of the 60- to 100-cow dairies have gone away in our territories,” says Scott Brown, sales manager with Cummings & Bricker, an equipment distributor that serves dealers throughout the Northeast, Mid-Atlantic and Midwest. Product lines include Jaylor TMR mixers, Teagle bale processors, and Weaverline TMR choppers. “But we still see pockets with strong Amish and Mennonite communities who still use wrapped or dry round bales as forage for their ration. There are also a lot of customers who maybe don’t farm full-time anymore, but still want to use their land. Our family farm is a good example. We still maintain a herd of 30-35 angus cattle. These types of smaller operations can really benefit from having a TMR mixer.”
Brown is also seeing more goat farms popping up. “A couple of them are Amish goat dairies,” Brown says. “Right now they’re just putting bales of hay in the pen so the goats can eat, and are feeding them grain separately in the parlor. They’ve been asking us if a TMR mixer is the right way to go.”
Dairy farmers tend to be Jay Monson’s most likely TMR buyers, but sales to the beef farmer business is growing. “And with dairies continuing to get bigger and bigger, we’re starting to see more customers who want two TMRs in their operation,” says Monson, store manager at Johnson Tractor’s Baldwin, Wis., location, which carries Supreme International and Meyer TMR mixers, along with grinder mixers from H&S Mfg. and Art’s Way.
Feed Mills Help Farmers Regain Control of Feeding Operations
Monson says some dairies, particularly those in the 60- to 80-head range, have also been making investments in grinder mixers to process their grain. Beef producers and hog farmers continue to be his biggest customer segments for grinder mixers, though. “We’ve actually sold 3 units to hog farmers over the past couple of years, even though that isn’t that big of a market around here,” Monson says.
Some dairy farms will also have a grinder mixer to complement their TMR mixer. One factor driving that trend in pockets throughout the country is a reduction in the number of feed mills serving an area.
“The feed mills that are still in business will often cater to large producers,” says Jordan Kriesel, product manager at H&S Mfg., a manufacturer of grinder mixers, roller mixers and bale processors. “That helps a company like ours because many of the smaller farmers and ranchers are looking to produce their own feed. With some of our customers, a grinder or roller mixer is the only way of getting food to their animals.”
That same trend is helping to drive demand from other key customer segments.
“A lot of smaller hog farmers also do row crops,” Kriesel points out. “Instead of getting a truckload of feed, they’re looking to just grind their own feed with their own corn, or whatever their forte happens to be. And it’s not just hog farmers. We’re seeing this with beef and dairy producers, and even chicken farms.”
With respect to vertical TMR mixers, Schams liked to draw attention to the gearbox. “A gearbox is rated off of torque,” Schams says. “Supreme has always seemed to go with one that was twice what they really needed. But that way they knew there would never be a problem.”
At the end of the day, Countryman reminds, TMR mixers are for the final delivery stage — completing that final processing of forages to get them down to 2 or 3 inches, and mixing them with grains and supplements. For farmers raising ruminants, that grain has to be preprocessed before it goes into a TMR mixer because most ruminants can’t handle most of the starch. “This is where equipment like roller mills and hammer mills can come into play,” Countryman says.
Equipment that preprocesses forage material, such as bale processors, can also come into play.
“We see it with some large dairies that are doing 10-12 loads per day in their TMR mixer, and don’t want to spend the 4-7 minutes it takes to process a bale,” Countryman explains. “They’ll run several bales through one of our Teagle bale processors, and then dump that in the TMR. Then as quickly as they can add other ingredients to the mixer, the ration is mixed. It’s all about saving time.”
Gaining Ground with Grinders
Whereas TMR mixers often sell to existing users, Monson says half of his store’s grinder mixer sales are landing with first-time buyers. The hog farmer segment is huge, followed by beef producers and even dairy farmers. Monson points to feed mill attrition as a big reason why this market seems to be growing.
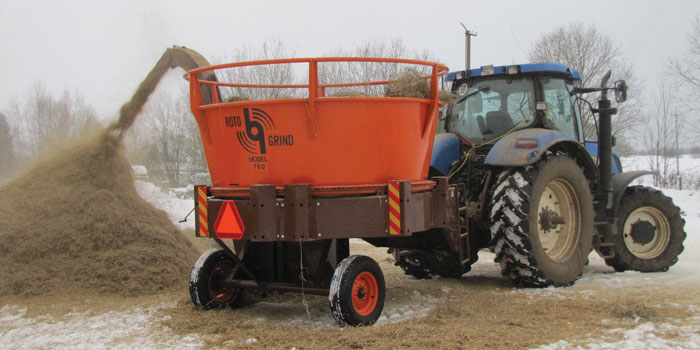
Roto Grind tub grinders feature hammers and adjustable shear plates, enabling farmers to grind any type of forage down to the desired size. Then that product can be loaded into a TMR mixer to speed up the final mixing process. Pictured here is the Model 760, which can deliver anywhere from 5-40 ton per hour depending on various factors including tractor horsepower, material type and size, and how fine the material is being ground. Roto Grind (Burrows Enterprises)
“There used to be a feed mill in every town,” Monson relates. “Now there are only a handful in our area. If a farmer wants to buy their feed, it has to get trucked to them, which doesn’t always happen at the most convenient times. If they have a grinder mixer on their farm, they can mix their feed whenever they’d like. Plus, they may have their own corn, beans or oats they’d like to grind themselves so they know exactly what’s going into their ration.”
Unlike with a TMR mixer, forage is not added to the mix with a grinder or roller mixer. This equipment is used exclusively to process grain. With some units, farmers can also incorporate minerals through an integrated supplement tank to improve the quality of the final mix.
A grinder mixer and roller mixer ultimately do the same thing. That said, a roller mixer tends to provide a more consistent grind compared to a hammermill, according to Jordan Kriesel, product manager at H&S Mfg., a manufacturer of grinder and roller mixers. A roller mixer has two big drums that turn, cracking the grain and creating a more powdery mix that dairy farmers tend to prefer. A hammer mill can get to that same powdery consistency by adding screens inside.
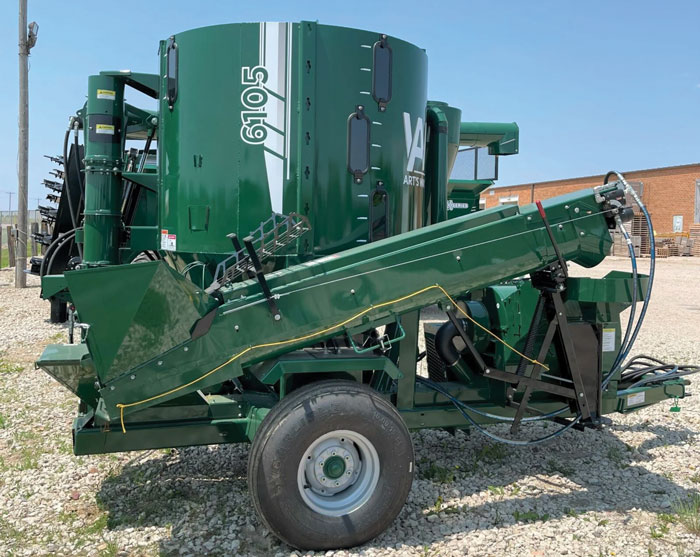
All of Art’s Way’s hammer mills feature 4-way reversible knives to get more use out of this common wear item. Customers can choose between a 20 or 26 inch hammer mill size to match the output they desire. A throat magnet prevents metal debris from staying in the feed through processing. A balanced rotor assembly keeps the mill operating smoothly. Art’s Way
“Roller mixers cost a little more money,” Kriesel points out. “So for the farmer, it really comes down to how consistently they want their feed ground.”
The dealer can also help the farmer determine which size roll they need. H&S hammer mills, for example, have a screen the feed must pass through. There are 10 different mill screen sizes ranging from 1/8 to 2 inches. The dealer should always ask the customer what their preference is. There are also different styles of infeed augers, i.e. a standard auger and one designed for cob corn. Optional auger extensions are also available so farmers can reach taller grain bins.
Helping a farmer choose between a grinder mixer and roller mixer largely comes down to their personal choice. “Most of our customers already have their minds made up when they come to us,” Monson says. That’s not to say a dealer shouldn’t take the opportunity to talk about the unique features of the products in their showroom.
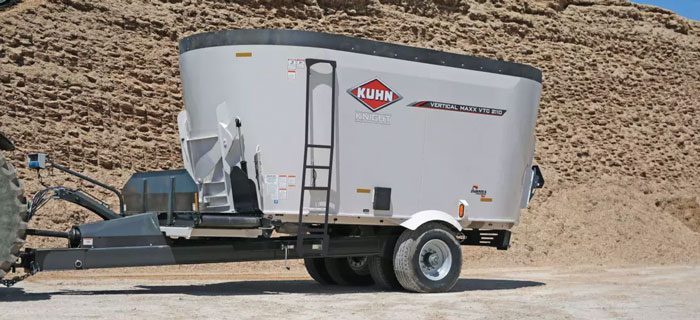
Kuhn Knight VTC 200 Series Vertical Maxx twin-auger commercial mixers are built to the heaviest specifications in the industry to ensure a quality mix, even in the most extreme-duty cycles. With commercial-grade components, stainless steel liners standard and the heaviest single-stage planetary gearboxes in their class, these mixers are built to withstand any feeding application and are designed to continue running around the clock. Kuhn
“H&S, for example, has implemented some key improvements on their grinder mixers,” Monson says. “These mixers are hydraulically driven. They’ve went with a bigger hydraulic tank to dissipate heat better. They’ve also gone to larger tires, which helps customers who have to travel between farms.”
A farmer may also benefit from specialized grinding equipment that processes not only grains, but also forages. Roto Grind manufactures this type of equipment. Their grain grinders are designed for processing any type of grain. Their tub grinders, on the other hand, allow for the grinding of forage, along with ear corn, shelled corn and smaller grains.
Troy Keast is a Roto Grind dealer. When selling grain grinders, he likes to focus on the unique engineering aspects that allow these units to deliver a mix consistency that’s appealing to dairy farmers. He’ll typically sell them in the fall to customers with high-moisture corn.
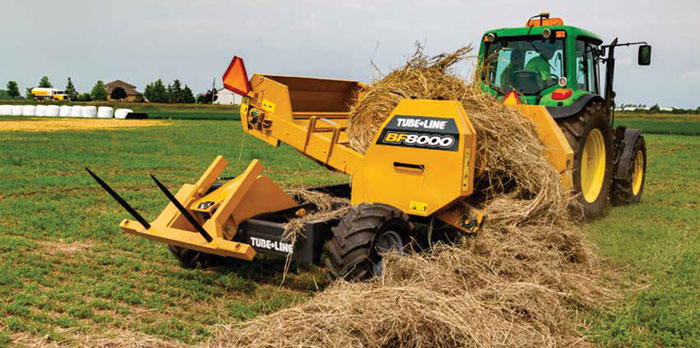
Tubeline’s BF8000 utilizes an apron chain and a rotating drum with retractable fingers to unravel and fluff round bales. The self-loading model trails behind the tractor and can carry two bales. A stationary model is also available and makes quick work of unraveling bales to re-bale them for other markets. An optional square bale conversion kit can be fitted to the BF8000. Tubeline Manufacturing
“The Roto Grind grain grinder has the same hammer mill and shear plates (as opposed to screens) as the tub grinder, but the grain grinder also has a top with additional shear plates,” says Keast, senior sales representative at Keast Enterprises in Henderson, Iowa, an equipment dealership whose lines include Roto Grind and Art’s Way grinder mixers, and Meyer and Penta TMR mixers. “Also on the grain grinder, the knives needed to shred hay are removed and replaced with additional hammers. There’s also a fine-grind corn kit available with even more hammers to really get to that fine powdery mix dairy farmers like.”
Selling the Roto Grind tub grinders is more involved due to the complexity of grinding a variety of forage materials. Keast has developed a list of questions to help steer conversations in the right direction.
“The biggest thing is how much horsepower the customer has,” Keast says. “Horsepower is everything no matter what you’re grinding, but especially grasses and wet material. I like to see 100-240 horsepower. A tub grinder will work with 80-90 horsepower, but it will run slower than most of our customers would like. The closer to 240 horsepower, the better.”
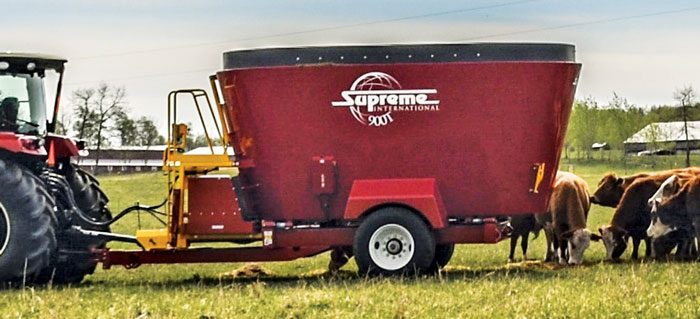
Supreme’s 900T Vertical Mixer has a maximum payload capacity of 24,000 pounds and requires 130 hp. Like all Supreme vertical mixers, it’s built for durability. The company says it features the heaviest two-stage planetary drive available, combined with a heavy-duty gearbox, to enable the auger to rotate through the toughest of materials. Supreme International
Keast also likes to find out what the farmer is feeding, be it dairy cows, beef cattle, calves, sheep, etc., because that dictates material size. Taking it a step further, he likes to determine what they are feeding those animals, be it corn stalks, alfalfa, or perhaps prairie grass or ditch grass.
“You set the grinder to the size of the product you want to feed your animals,” Keast says. “You could set it up for a corn stalk bale and wind up with a 3- to 4-inch length. If you kept that same setting and dropped a high-quality alfalfa bale in there, that final material will be 1-inch, at best. So I always take time to explain how you really have to set the grinder to whatever you’re grinding and whatever you’re trying to feed.”
One thing Roto Grind prides itself on is the ability to grind dry or wet. That’s another thing Keast takes into consideration when counseling customers.
“If a farmer plans on doing a lot of wet grinding, I like to stress a higher-horsepower tractor, but push the smaller tub grinder (Model 760) because it has a smaller 7-inch mill and takes a smaller bite,” Keast explains. “If you try to put wet forage in a tub grinder with a 10-inch mill without a high-horsepower tractor, you’re going to lay it on its knees.”
As you can see, there are several types of feed-processing machines available. Each has a fairly straightforward job to do, and each does that job in a slightly different way. By taking the time to understand the customer’s current feeding operation and how they’re hoping to improve it, dealers can better match the right solutions to the application, helping customers ensure that both their animals and bottom line receive the nourishment they need.