When the 2018 Farm Bill removed hemp from the controlled substance list, there was a lot of excitement over the potential of this “new” agricultural crop. Vote Hemp, a grassroots lobbying organization, even suggested that the land mass used to grow hemp could reach upward of 200,000 acres in 2019. They weren’t far off. Planted acreage reported to the USDA Farm Service Agency tallied up to 146,065 acres.
Then reality started to set in, as is sometimes the case when the excitement of an emerging market dies down. The USDA National Hemp Report released in April of this year shows that acreage had shrunk by 63% by 2021. Acreage decreased another 48% in 2022, followed by another small reduction in 2023 to a level of just 27,680 acres.
“Hemp CBD was the modern day gold rush in 2019,” says Sam Berthiaume, commercial sales at Champlain Valley Equipment with 5 locations in Vermont. The dealership’s equipment lines include Kubota, New Holland and Case IH, along with numerous shortlines including Orkel, which manufactures high-density baling equipment that’s well-suited to hemp. “The market got flooded so fast that growers almost couldn’t give the stuff away. A lot of guys walked away empty handed.”
Takeaways
- The potential for hemp is still there, but growers need pre-established contracts with buyers and processors before assuming the risk.
- Farmers growing hemp for the grain may already have the necessary equipment, though hemp-specific seed discs (if using a regular planter) and draper heads on combines can provide an advantage.
- Farmers growing exclusively for fiber can benefit from unique cutting equipment to size the tall hemp stalks down, as well as baling equipment that can handle those stalks that have a tendency to twist and wrap.
- Farmers growing CBD hemp can benefit from having a transplanter to reduce the labor involved with planting, as well as specialized harvesting equipment.
Berthiaume grew up on a dairy farm. He was also one of the first farmers in Vermont to participate in hemp trials.
“I did 13 acres of industrial hemp (for fiber and grain) in 2017-18 on my cousin’s farm,” Berthiaume says. “We actually had a very successful crop. Then after 2018, I got together with some friends to start CBD farming. That’s when the market exploded and soon crashed. I switched gears and took a job at the dealership in December 2020.”
Hemp hopefuls like Berthiaume are optimistic that the market has stabilized. USDA data actually shows that a dozen states saw a rebound in hemp acreage in 2023, including California, Idaho, Illinois, Kansas, Maryland, Minnesota, New Jersey, North Carolina, Ohio, Oregon, Pennsylvania and South Dakota. It’s a positive trend in an industry segment that could use some positivity.
Top Hemp-Producing States
South Dakota – 3,200 acres
Montana – 2,900 acres
Oregon – 2,300 acres
California – 2100 acres
Missouri – 1,750 acres
Colorado – 1,350 acres
Kentucky – 1,310 acres
SOURCE: USDA National Hemp Report, ISSN 2831-5545, released April 17, 2024, by the National Agricultural Statistics Service (NASS), Agricultural Statistics Board. Acreage based on 2023 data.
Is the Future in Fiber & Grain?
Another trend has emerged regarding what farmers are growing hemp for.
Initially in 2019, most of the hype was around CBD. Now, the number of acres harvested for fiber has grown 77% over the past couple of years. In fact, nearly half of the hemp acres harvested are for fiber now. Floral (CBD) is second at 30%, followed by grain and seed at 16% and 5%, respectively.
“I’ve been doing this for 30 years, and I believe the long-term prospect for this crop is around the fiber and grain,” says Eric Steenstra, president of Vote Hemp. “Hemp grain has huge potential as a food source for a variety of animals. Demand for seed oil is strong, too. As for hemp fiber, a huge driver is sustainable home construction for things like flooring.”
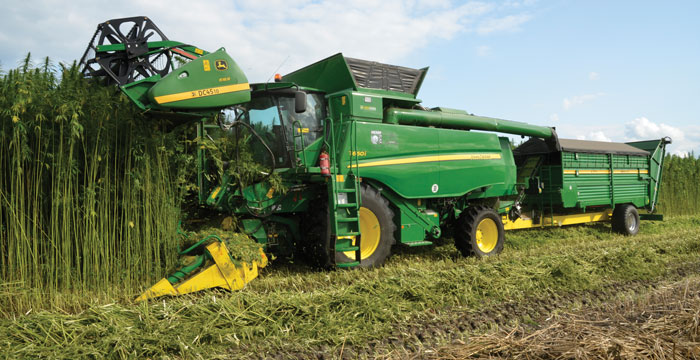
CANN Crop Solutions provides equipment that can harvest every part of an industrial hemp plant. Its DoubleCut Combine (pictured) can harvest and separate a complete plant. “That gives the cleanest product streams possible, leading to higher-quality fiber, seed and leaves,” says Gerard Hosper, business development at CANN Crop Solutions. CANN Crop Solutions
“I would love to see us stop using Chinese bamboo, and replace that with American-grown hemp,” says Ryan Given, product manager at ACI Distributors based in St. Charles, Mo., whose products include McHale hemp balers. “From what I’ve heard, hemp fiber can be a viable alternative for things like paper and other pressed materials. Hemp fiber is some wicked stuff.”
Vote Hemp thinks a redefining of hemp is an important step in encouraging farmers to begin increasing their hemp acreage again. Vote Hemp has actually launched a petition urging Congress to do just that.
“We need Congress to change the definition to allow up to 1% THC,” Steenstra says. “If a farmer is growing hemp for the fiber and grain, it’s pretty clear they aren’t after the flower and cannabinoid (THC, CBD). Farmers have enough risks already. We don’t want to see them have to destroy a crop because it’s slightly over the current limit of 0.3%. There has already been some legislation introduced, so I’m very hopeful the definition will change.”
South Dakota, which has become the top hemp-producing state in the country, minimized its own risk by not jumping the gun too early. Growers didn’t even start planting hemp until 2021 when 1,850 acres were planted. That acreage grew to around 3,200 by the end of 2023, a 73% increase over a 3-year period. And according to hemp grower and advocate John Peterson, hemp is overwhelmingly farmed for fiber.
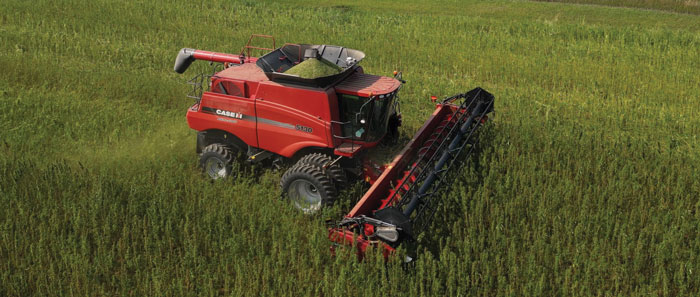
John Peterson uses an old Case IH 5130 combine to harvest industrial hemp grain. Dakota Hemp
“Growing for fiber is completely different than CBD,” says Peterson, owner of Dakota Hemp in Wakonda, S.D., a company that farms hemp and uses it to develop hemp-based retail products. “A lot of the equipment that’s needed is already on a farm. So hemp is readily accepted by large-acre farmers already.” Peterson is also the secretary/treasurer of the South Dakota Industrial Hemp Assn. (SDIHA).
Another key to the sustained success in South Dakota is that farmers have a place to take their hemp bales. Ken Meyer, current president of the SDIHA and vice president of Complete Hemp Processing in Winfred, S.D., got his processing plant operational in 2023. Now Peterson is getting his own up and running.
“Before Ken and I decided to put our processing plants up, the closest place for a farmer to take their bales was Montana or Kansas,” Peterson says. “Hauling round bales a thousand miles is not feasible to the pocketbook.”
“You want to grow the hemp plant [for fiber] tall like bamboo, and then cut and bale it before it puts seed on. The challenge is that you don’t want to run too much long, fibrous material through a rapidly rotating machine…”
Having reliable local processors they could sign contracts with gave South Dakota growers the confidence to start putting industrial hemp seed in the ground. It also helped that there was a reliable hemp seed salesman who was active in the state, Derrick Dohmann of Horizon Hemp Seeds. In other words, the horse has stayed ahead of the cart in South Dakota, allowing the industrial hemp industry to establish itself in a more sustainable way.
Equipment for Industrial Hemp
When growing hemp for fiber, farmers often use a grain drill to plant seed, which Berthiaume can attest to. When he planted his 13 acres of industrial hemp back in 2018, he used a 7-inch grain drill. He taped off every other hole to plant 14-inch rows.
Planters can also be used, though certain modifications may be necessary. For instance, Great Plains developed a specialized hemp seed disc for its PL Series and Yield-Pro Planters. Industrial hemp seed can be difficult to accurately plant due to its unique shape and weight. Great Plains’ hemp seed disc has several design elements to achieve more precise seed placement, such as optimized hemp pockets, large-diameter wheels that rotate more slowly, and positive air metering for more uniform spacing.
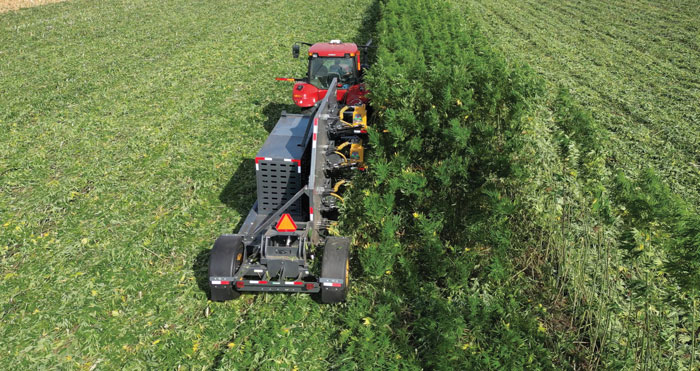
John Peterson uses a Bish FiberCut to cut tall industrial hemp stalks into several more manageable pieces. Dakota Hemp
Harvesting an industrial hemp plant can also present some challenges. When harvesting for both fiber and grain, where a grower will typically allow the plant to grow 5-8 feet tall, Peterson has been using a standard combine with large round-bar concaves. He sets it as high as it will go to clip off the top 1-2 feet of the plant to harvest the seed. Peterson has had success using a mid-size combine with a 30-foot conventional platform bean head set in the wheat position. He’ll then come back later to chop and bale the remaining stalks.
When growing hemp for fiber (stalks) only, harvesting can get interesting.
“You want to grow the hemp plant tall like bamboo, and then cut and bale it before it puts seed on,” Peterson explains. “The challenge is that you don’t want to run too much long, fibrous material through a rapidly rotating machine. Larger combines can swallow a lot more, which helps. But the hemp plant is still roughly 25% moisture when you’re harvesting it, so you have to be careful.”
Peterson has been using a specialized piece of cutting equipment from Bish Enterprises called the FiberCut. “It’s a four-bar sickle bar cutter,” Peterson says. “Some fiber stalks can end up being 15 feet tall. Cutting them into four smaller sections allows them to lie on the ground better for faster drying, retting and handling. I don’t care what kind of baler you have, it’s probably not going to handle a 15-foot input.”
This is especially the case with a plant like hemp that has a tendency to twist and wrap. To that point, Peterson says growers can also run into issues when raking.
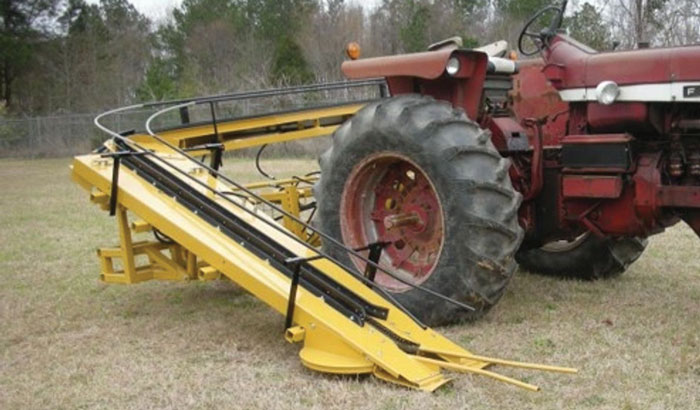
The Powell 6031 Hemp Harvester cuts CBD hemp plants at near ground level, and then properly orients them and sends them up a conveyor to a wagon or trailer pulled alongside the tractor-drawn harvester. Marco Mfg. Co.
“I’ve had good luck using rotary rakes (tedder style) so far,” Peterson relates. “The open-wheel rake is where farmers sometimes run into issues. We typically recommend putting plastic shields on the rake wheels, or running closed-wheel rakes. That will help keep those stalks from getting wedged in there.”
The same considerations must be made when attempting to bale hemp stalks. According to Given, experienced hemp growers do not go into harvest with the same baler they’ve been using for hay.
“At a bare minimum, you want a silage baler,” Given says. “The properties that make hemp a good fiber are the same properties that make it want to twist and wrap. With a silage baler, you’ll have some kind of scrapers designed to minimize buildup around the rollers.”
“I’ve been doing this 30 years, and I believe the long-term prospect for this crop is around the fiber and grain…”
McHale balers , Given points out, are built for handling silage. They have cleaning augers on the rollers and wear parts on essentially every area that touches the crop, which is important because hemp is also very abrasive. Then, McHale offers what it calls a baler hemp kit.
“You’re basically taking a 7-foot pickup and turning it into a 4-foot pickup by deleting the outer tines,” Given explains, adding that when a baler plugs, it’s usually around the corners, edges and feed augers. By removing those outer tines, you’re reducing the amount of crop that can be pulled into those problem areas. “That hemp will still wrap, but you’re extending the time when you’ll need to pull the machine down, take the stripper bands off, and start cutting hemp out of it,” Given adds.
Equipment for CBD Hemp
When growing CBD hemp, farmers are after the flowers. This requires a different approach to planting.
“You need strict seed control in order for the plant to make the proper flower for CBD,” explains Dan Timmer, owner of Mechanical Transplanter Co. (MTC). “You need feminized seed. If you end up with too many males in the field, it can ruin the whole crop. A grower is able to weed out those males in a greenhouse before taking them out to plant. Hemp seed is too expensive to throw a bunch of seed in the ground and hope it comes up female.”
Timmer is starting to see signs of a resurgence in the CBD segment of the market, albeit in a much smaller way than in 2019. Growers are being far more cautious now, often planting smaller fields of 1-5 acres. Still, Timmer says a transplanter implement can be a smart investment, even in these smaller applications. Compared to planting completely by hand, which some smaller CBD growers do, a transplanter will help save a considerable amount of backbreaking time. Labor cost savings could offset the price of a transplanter in just a season or two.
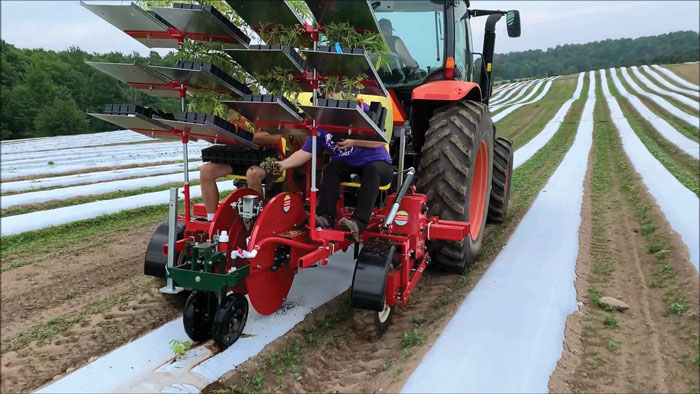
Mechanical Transplanter Co. offers carousel- and finger-style transplanters for planting CBD hemp in bare ground or plastic mulch/film. Pictured here is the Model 948 Mulch Transplanter. Mechanical Transplanter Co.
MTC manufactures both bare-ground transplanters and machines that plant through plastic mulch. Plastic mulch is popular because it helps with weed suppression. “CBD hemp growers want bigger plants and much wider spacing,” Timmer points out. “Some of these CBD hemp fields end up looking like Christmas tree fields.”
Whether planting on bare ground or through plastic mulch, transplanters are hand-fed so they still require human labor. It’s important for a dealer to develop an understanding of the farmer’s needs, as well as their experience using farm equipment in general. Many CBD hemp growers are not typical farm equipment operators.
Timmer says finger-style machines are simple and versatile. “They can handle a wide range of plug sizes, and can also do bare-root plants like onions, strawberries and sweet potatoes if a grower is also going to work with those types of crops,” Timmer says. “Finger-style transplanters require two people per row. A carousel-style machine is much faster and requires just one person per row. But carousel-style machines cost more and require the operator to be a bit more mechanically inclined.”
“The reality is, hemp can be a really good crop that gives farmers another way to make some extra income … Growers just need to be growing it the right way and for the right reasons…”
“In choosing a transplanter, a grower should consider speed, quality and versatility,” says Cameron Hill, director of North America at Global Ag Company, which specializes in Italian farm equipment including Checchi & Magli transplanters. “Is there a possibility the grower may want to plant in plastic and bare ground, and maybe even direct seed sometimes? Our Wolf Pro with SeedPro can do it all in one machine.” On the other hand, Hill adds, a faster carousel-style machine is a better choice if a grower is only looking to plant on bare ground.
Like planting, harvesting flowers from a CBD hemp plant is also sometimes done by hand. Combines with modified pickup headers can also work. There is also specialty equipment for harvesting CBD hemp.
“Our hemp harvester costs around $40,000,” says Tom Pharr, president of MarCo Mfg. Co., maker of the Powell Hemp Harvester. “We generally say a grower needs around 25 acres to realize a reasonable return. On 25 acres, a grower should save enough on labor to pay for our machine within 5 years.”
The Powell 6031 Hemp Harvester is designed to cut the stalk at near ground level, orient the stalk perpendicular to the direction of travel, and positively convey it by a special gripper chain to a wagon or trailer pulled alongside the harvester. The self-contained hydraulic system is powered by the PTO of the tractor carrying the harvester.
Powell was long known for its tobacco harvesters when some farmers asked Pharr if they would work with hemp. The tobacco harvesters did an OK job, but it became clear that modifications were needed in order to efficiently harvest hemp.
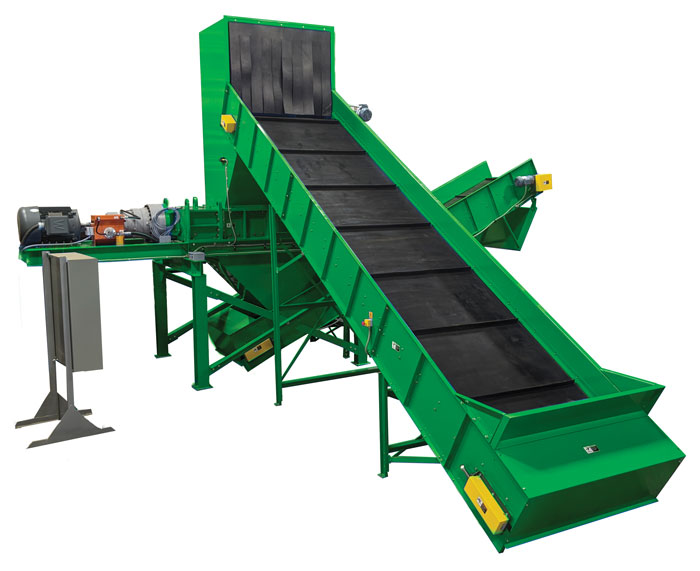
HY-Reaper processing systems can be configured to process full hemp plants from the field to aid in separation prior to the drying or extraction processes. Available in either stationary or mobile versions, these systems are designed to provide gentle handling and clean cutting to preserve final product quality. High Yield Solutions
“The biggest thing was making the harvester easier to transport,” Pharr says. “A lot of these CBD growers are working smaller fields and need a harvester that’s easy to transport from field to field. We also had to make some changes on the head and conveyor system to hold the plant a little better. Lead-ins were changed to better pull the plant in. A hemp plant is much smaller than a tobacco plant, so trying to get it stable in the harvesting system took a little bit of work. Our system has been working well ever since, and no other significant modifications have been needed since we were first figuring all of this out back in 2019.”
It has been a volatile market since hemp first exploded out of the gate in 2019. But the industry is showing signs of stabilization, and is offering opportunities to growers in the right circumstances where processors and equipment dealers are set up to support them.
“What happened to the hemp market may actually turn out to be a good thing,” Berthiaume says. “The quick crash helped weed out a lot of people who didn’t know what they were doing and were in it for the wrong reasons . The reality is, hemp can be a really good crop that gives farmers another way to make some extra income. Hemp also helps clean the soil to improve soil health, which is good for everything. So there are a lot of benefits and a lot of opportunity. Growers just need to be growing hemp the right way and for the right reasons.”