A visit to the American Foundry Society’s Metalcasting Congress last week in Milwaukee turned up equipment design news for Nebraska-based Orthman Manufacturing, and ductile iron casting supplier Lethbridge Iron Works of Alb., Canada. An independent panel of judges recognized the Lethbridge part as the “best example of a casting conversion” and was on display for AFS’ national event that drew close to 3,000 attendees. It was also the only ag equipment application honored among the annual Casting of the Year program.
Dylan Bruins, Business Development Lead of Alberta-based Lethbridge Iron Works, described the award-winning row cleaner shoe application. “It’s a component to hold a pair of concave ground-engaging discs at a specific angle for crop residue removal and features holes to adjust the disc width based on field conditions. The entire assembly pivots about a cast hole with design features to attach a constant-pressure assembly.”
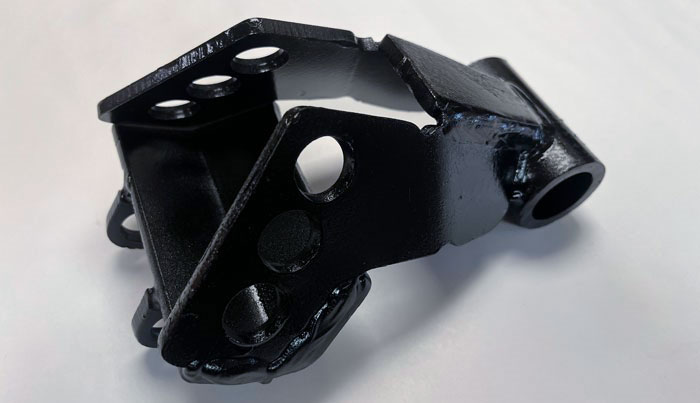
The prior weldment design required 7 individual pieces
Previously designed as a weldment, the assembly had required 7 pieces, including 6 laser-cut plates, 3 of which are then formed with a brake – and 1 tube. In total, there were 16 weld segments that were tedious to fixture and a challenge to maintain dimensional consistency. It was also costly to produce due to materials, laser cutting and welding labor.

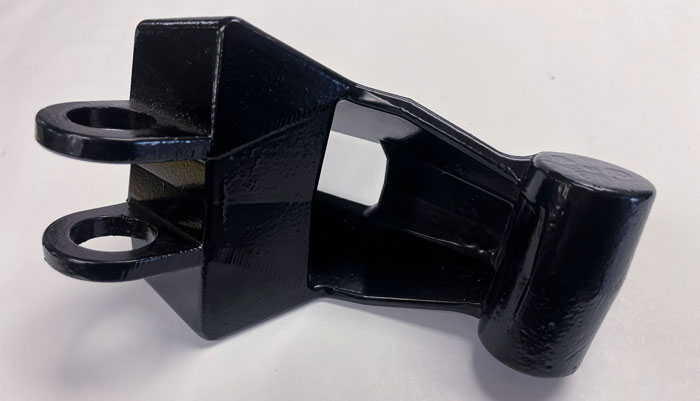
Cast Design: Through casting, the iron could be placed exactly where it was needed.
Material: Ductile Iron Grade 65-45-12 … Casting Process: Green Sand Molding (Hunter 10) … Weight: 7.3 lbs.; 6 lbs. machined … Dimensions: Approx. 8 in. x 7 in. x 6 in.
“The fabrication was functional, but was labor-intensive, expensive and difficult to maintain dimensional consistency,” says Bruins, “Seven pieces required 7 individual part numbers and an assembly number to maintain in inventory. There was also a desire to purchase a single-cast part that could exceed the performance of the fabrication at a reduced total per-piece cost.”
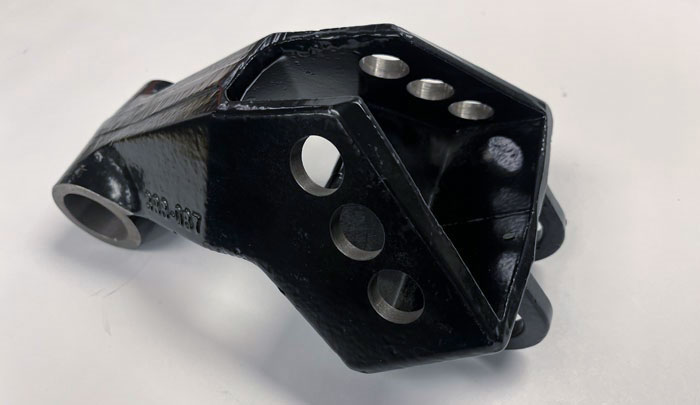
Machined Casting Design
In the move to design the unit as a one-piece casting, several considerations were made:
- Both the cores and the casting itself were designed for manufacturability in Lethbridge’s process.
- It was designed with the internal geometry cored, with the main boss and 6 adjustment holes machined in.
- The “pin tab” features were not dimensionally critical and were therefore cast in without machining.
- The “as-cast” pin tab also provided a natural hanging point for the powder coat line.
According to Bruins, the casting offered:
- Significant labor savings vs. the fabrication
- Part number and manufacture date cast into the part itself
- Eliminated dimensional variability
- A single part number to maintain in inventory
- Finite elemental analysis showed a yield strength increase of more than 2-fold
- Parts were received machined and powder-coated with a bushing pressed into the main bore, saving internal labor for pre-assembly.
- Total cost savings of more than 35%
For more information on designing and purchasing cast metal components, visit the Casting Source at www.castingsource.com and Lethbride Iron Works at www.lethiron.com