Do you know what tire pressure you’re running in your tractor tires?”
That’s an informal question Nate Firle asks of growers at conferences and workshops where he speaks as owner of AgRevival, a Minnesota agronomic research firm located in Gibbon. The answers he’s recorded over the years can be surprising, but they demonstrate some low-hanging fruit is going unharvested on many North American farms.
Proper ag tire inflation on tractors, planters, sprayers and combines has been securely linked to improved corn and soybean yields through reduced compaction, and recent in-house studies by Firestone Ag show properly inflated tractor tires can mean significant improvements in overall productivity through boosts in “acres worked.”
Firle says his “conference research” convinced him 50% of growers have no idea what tire pressure is in their tractor tires at any given time.
“They look at a tire and if it doesn’t look flat it’s probably good to go,” he explains.
“About 20% have a rough idea of their tire pressures, and if they don’t know it they are confident they have records to consult before they go back into the field,” he says. “And,10% know exactly the pressures they need to run on the tractor, the planter, the sprayer or the grain cart.
Footprints in the Field
At a recent grower field clinic, Firestone Ag representatives made on-site comparisons of varying tire inflation pressures with paint footprints on standard vs. VF designed ag tires. Using the same tractor, the tires were “foot printed” to illustrate the difference in ground-contact and loads on the tire and axle as inflation pressures decreased.
“The other 20% also know exactly what tire pressure is in their tires — and are quite confident and proud of the fact as they tell me it’s exactly what’s printed on the sidewall.”
The reduced compaction and improved daily productivity benefits of proper tire inflation likely won’t be found at work for the last group, he chuckles.
At nearby NTS Tire Supply in Redwood Falls, Matt Schroepfer says once growers begin to experience the benefits of reduced compaction and improved power transfer to the ground, they begin to look beyond the tractor and apply that knowledge to their other equipment.
“It’s fun and fulfilling to see that kind of growth response from growers as they get turned on about tires — regardless of how boring tires may seem at first,” Schroepfer explains
Reduced Compaction Bonus
Working with Firle over a 3-year study from 2021-23, Schroepfer, NTS’s R&D and marketing lead, says the replicated AgRevival results compared 5 different tire pressure levels.
“We tested the maximum PSI that’s written on the sidewall, which in the case of the Alliance Agriflex VF tires (on the tractor and planter) was 35 psi, then we dropped it down to 28, 20, 12 and 6 psi across all the tires, then measured yield responses to the variable tire pressures,” he explains.
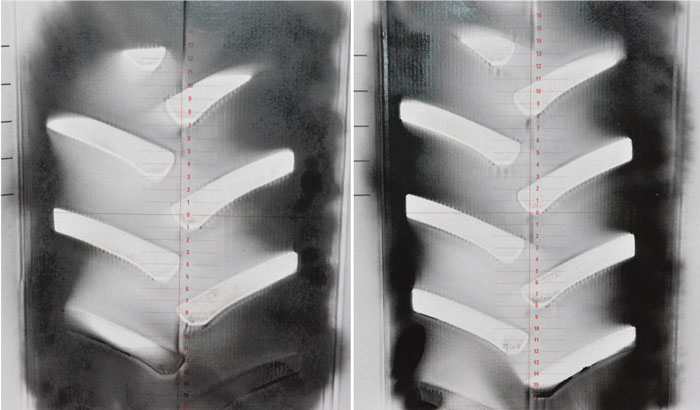
HIGH FLEXION FOOTPRINT — When these VF rated tires were compared, the 9 psi footprint was 5.5 inches longer than the 20 psi measurement and both results indicated far better compaction-reducing field performance than either of the standard tire comparisons.
The test was run with Firle’s 7R tractor loaded to 34,000 pounds with extra weights and a fully-filled 300-gallon liquid tank up-front to simulate an 8R machine that many in the Midwest use for corn and soybean production. The planter, however, was an 8-row box design and is much smaller than a large center-filled planter.
“While the planter was smaller, we still saw a proportional response, and I would expect to see a greater response with larger planting equipment,” Schroepfer explains.
Firle says the test was one of the most consistent studies he’s seen on his farm.
“For every reduction in tire pressure the yield for both corn and soybeans increased,” Schroepfer says. “It varied from year to year but remained very consistent.
“Once averaged over the 3-year study, going from 35 psi to 6 psi on the tractor and planter we saw an additional 7.5 bushels of corn and 3.4 bushels of soybeans. The results were evenly stair-stepped with each reduction in air pressure.”
“For every reduction in tire pressure the yield for both corn and soybeans increased…”
In a 2-year (2022-23) corn study by Beck’s Practical Farm Research (PFR) with sites in Indiana, Minnesota, Ohio, Iowa and Kentucky, overall averages of reduced planter tractor tire pressures showed similar results.
The PFR study included “Sidewall” pressure of 35 psi and dropped to 28, 20 and 12, with technicians explaining not all ag tires can be operated safely at 6 psi.
The average results of the multi-site experiments were as follows:
- 35 psi 217.6 bu./acre
- 28 psi 220.2 bu./acre
- 20 psi 219.8 bu./acre
- 12 psi 219.9 bu./acre
Schroepfer says these studies are just the latest in many experiments that have shown field compaction is a yield robber.
“The results just add to what is becoming common knowledge, and that is when we are squishing, compacting, the soil we’re losing yield,” he explains. “These tests, however, show how simple it is for growers to take steps to avoid those losses.”
Field Productivity Edge
In what must have looked like a tractor drag race, Firestone Ag recently staged a tire inflation test that showed the amount of air in tractor tires not only can affect compaction rates in the soil, it can make a significant change in how much soil a grower can work in a day’s time and how much diesel fuel it can save.
The test involved a pair of identical test tractors with identical standard tires connected by a cable and pulley system to a third “load tractor” (not running) equipped with a 23-foot field cultivator. The only variable for the test tractors was tire inflation — 15 psi for one and 30 psi for the other.
“As the tractors moved down the 1,000-foot test course, the tractor with lower tire pressure (and larger ground footprint) was able to pull ahead of the tractor inflated at near maximum pressure,” explains Dusty Hininger, field training manager for Firestone Ag. “At the end of the course, the tractor with lower tire inflation pressure was more than 50 feet ahead of the other tractor.”
Hininger says lower tire air pressure alone was responsible for the difference in traction — a difference that can add up to increased productivity in several ways.
“I would expect to see a greater response with larger planting equipment…”
With both tractors moving at 6 mph, burning 16 gallons of fuel per hour with diesel fuel prices pegged at $4.50 per gallon, over a 1,000-acre field, he says the properly-inflated tractor can cover 16.73 acres per hour compared with the over-inflated tractor which will cover only 15.89 acres in the same time.
Over 1,000 acres of field work, the difference amounts to more than 50 gallons of diesel burned by the over-inflated tractor compared with the machine running lower tire pressures, Hininger explains. “Also, because of better traction and additional ground covered, the ‘lower-pressure’ tractor will finish its job in 3 hours and 15 minutes ahead of the other tractor.”
Hininger says the test shows the simple practice of reducing tire air pressure during field work can equate to more than $226 in fuel savings and more than $63 per hour in operator time, based on a $20 per hour rate.
The test was repeated comparing standard tires with high-flexion tires and yielded even more time and fuel savings from the larger footprint available through the tires with flexion technology.