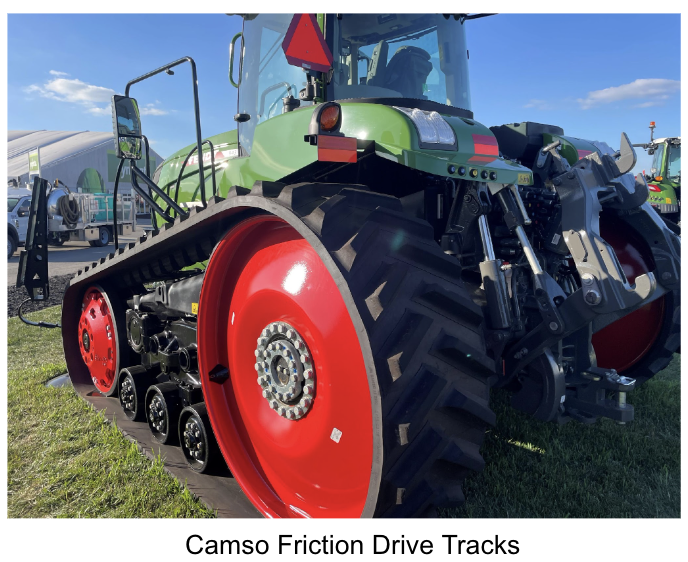
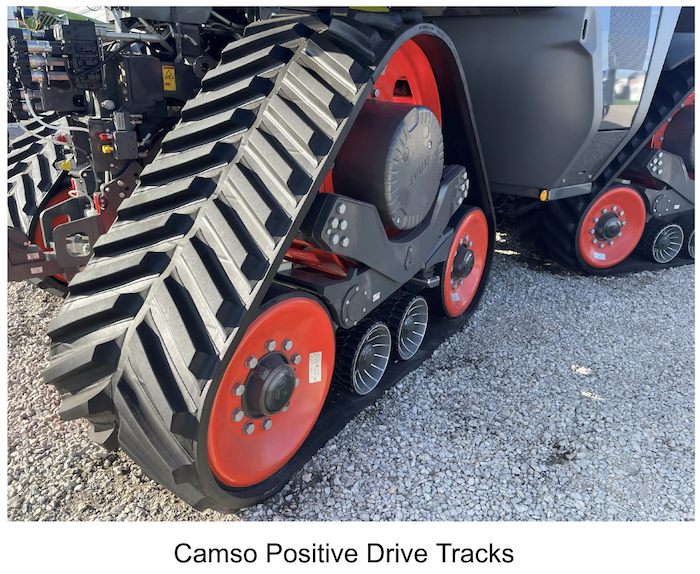
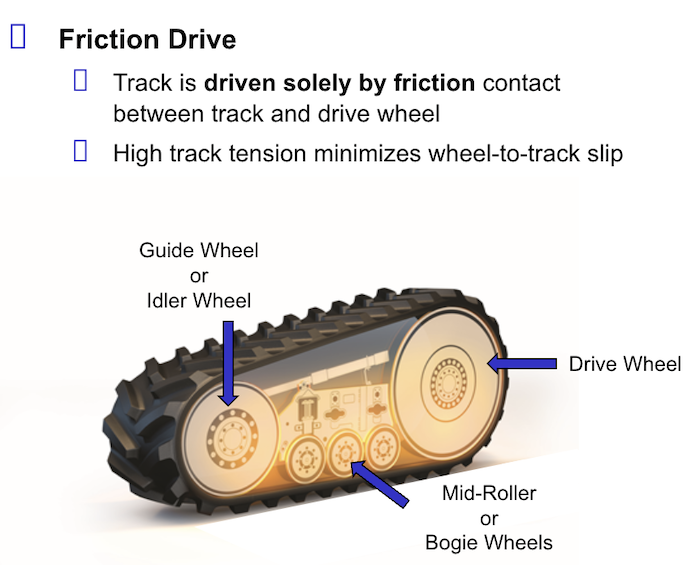
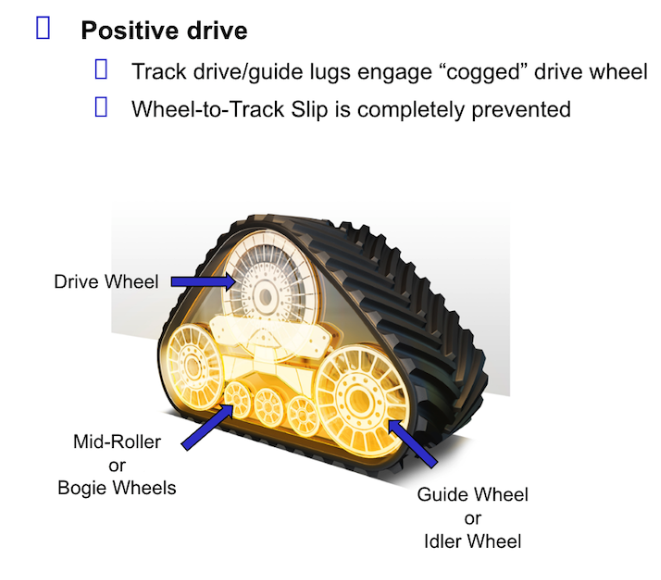
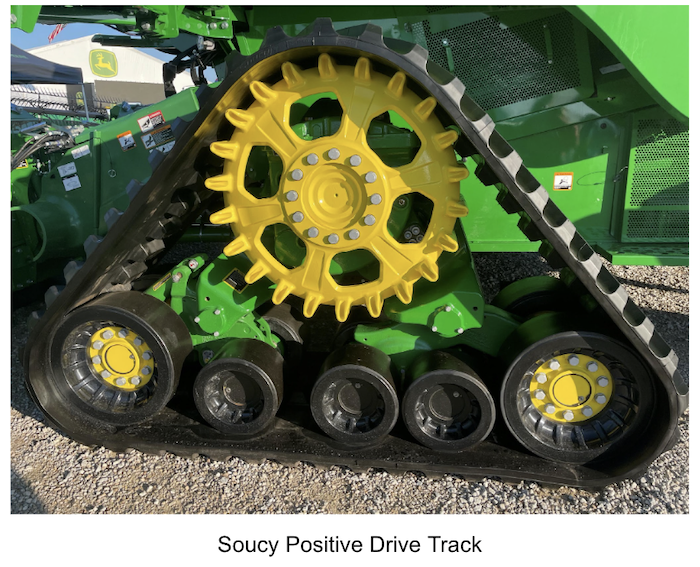
- Are similar in construction.
- Have an integrally wound main cable (zero cable) continuously from one side to the other, for strength.
- Rubber outer drive lugs for traction.
- Have a smooth roller path for the wheels to transfer weight of the machine to the ground.
- Have differing layers of steel and synthetic fabrics for strength in different applications.
- Friction Drive tracks have Guide Blocks, Positive Drive tracks have Drive Blocks.
- Fairly simple. Two guide wheels, two drive wheels, a track, and bogie wheels to support.
- Typically have less problems with the undercarriage.
- Last much longer as there isn’t as much adverse contact between the components.
- Friction Drive tracks (two tracks) are harder to ballast front to rear with cyclically loaded equipment.
- Friction Drive tracks lose much of its internal traction when moisture levels are too high (mud and/or water) resulting in difficulty maintaining forward direction or steering at times.
- More torque to the ground in difficult or high traction situations.
- Better control maintaining direction and turning in wetter conditions.
- Much lower lifespan than friction drive.
- Typically more problems with the undercarriage.
- Drive lugs are the workhorse of this track. Damage to the drive lugs from alignment, material ingestion, or over pulling greatly diminishes life expectancy of the track.
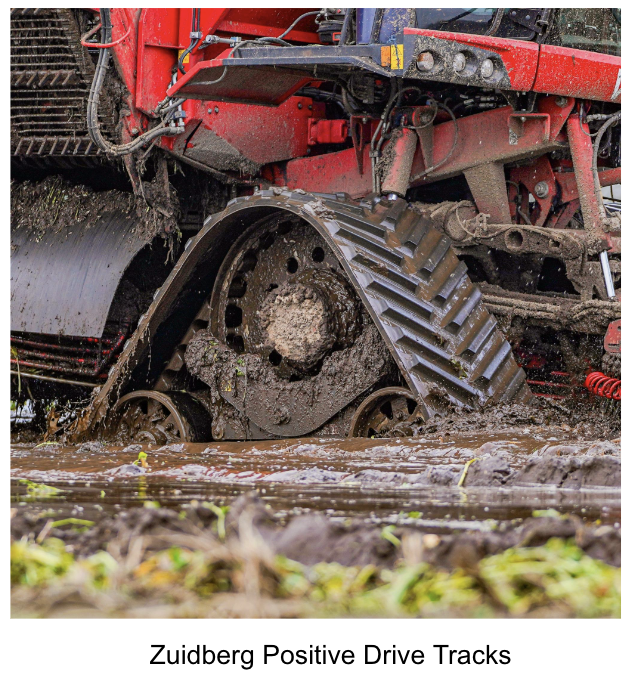